Factory Tours Shed Light on the Quality, Affordability of Today’s Manufactured Homes
MHVillage recently accepted an invite to Northern Indiana for a pair of extremely enlightening factory tours. Of the multiple factories to tour available, we choose Fairmont Homes in Nappanee and Clayton Homes at Wakarusa.
We want to share these great factory tours here with you!
Industry veteran George Allen began organizing the Manufactured Home Seminars and Factory Tours three years ago. He conducted them this year in collaboration with the Indiana Manufactured Housing Association.
The association will take over curating the event next year and for the foreseeable future.
Factory tours are organized to help educate community owners, in particular. However, they were kind enough to include some of us marketing and media types too! The idea is to better convey the efficiency and quality of modern manufactured homes. This is true for the construction process as well as the finished product.
The manufactured housing seminars helped manufactured housing professional understand how to buy directly from the factory.
The Sites and Sounds of a Manufactured Home Factory Tour
We were certain to take many photos and video in order to bring you the sites and sounds of a modern, efficient manufactured home factory.
So let’s get started at the lone location Fairmont Homes uses to turn out homes. The company started in 1971. Fairmont was run by the Shae brothers, Jim and John, until 2015 when Cavco Industries purchased the company.
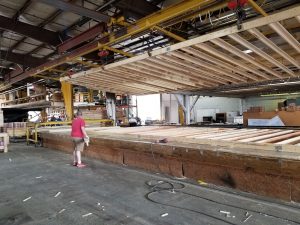
Joe Viglione, the general sales manager for Fairmont, led the tour for our MHInsider folks. Also along for the tour was a pair of owner/operators from Choice Properties, Rob Shouhayib and Michelle Hatfield.
We started in the floor factory. The floor plant is one of three on-site that employs about 200 people. All together, they cover 90,000 square feet of manufacturing space.
One of the quality control measures Fairmont Homes implements is the inclusion of “ladder ends” on the floors. This works as a buffer between the home’s plumbing and outdoor conditions.
Plumbing and electrical wiring are installed during floor construction rather than at the end of the home build. This makes it easier on workers who otherwise would have to access tight spaces. And it would mean more clean up at the finish. With aspects of the the home finishing done in-line with construction, home comes out cleaner. The process keeps the factory in a much more safe and orderly state.
“We use all oak flooring and it’s all interlocked for a much stronger floor than you’d get otherwise,” Viglione explained. “And when all the floors are completed, the seams are sanded flat for a better surface and also noise reduction.”
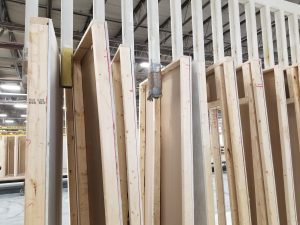
The home enters the assembly plant
Flooring is finished prior to the assembly stage, which is the install of walls and other vertical components. Major fixtures, appliances and some cabinets are installed. Again, the earlier iteration for these home amenities, such as Fairmont’s standard single piece fiberglass tubs, increases ease of installation for the builder. And it allows any difficulties with installation to be addressed before the home is near the end of the line and being prepped for transportation.
While the single piece tub is standard, all types of upgrade options are available. Rob Shouhayib asked about changes that would aid in access for people with disabilities or older residents.
Viglione said 36”-wide interior doors are available for homeowners who use a wheelchair or other assistance devices, and that surface levels and access to bath and show can be altered as well.
Some Cabinets, Appliances and Fixtures Go in Before the Walls
All of the Fairmont homes are built in batches, so the same product is moving down the line at the same time. With a single builder engaged in the construction of homes that move side-by-side, the ease of building and time efficiency is increased.
So, single sections are built side by side in a run. Later, the same line might take pairs of multi-section homes. Meanwhile a separate line of workers are building Fairmont park models or modular homes.
The saved time during the in-line building process give the homes an extra day to settle,
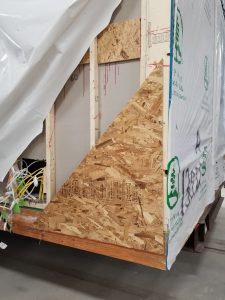
dry and cure — full two days to sit rather than shipping after a single day with increased risk of something moving, cracking or coming apart.
Fairmont also use 90-degree OSB corners for added home integrity during shipping.
The Fairmont Homes factory runs 220 days a year and produced eight homes a day — That’s about 1,760 homes per year out of a single location.
Clayton’s New Wakarusa Factory
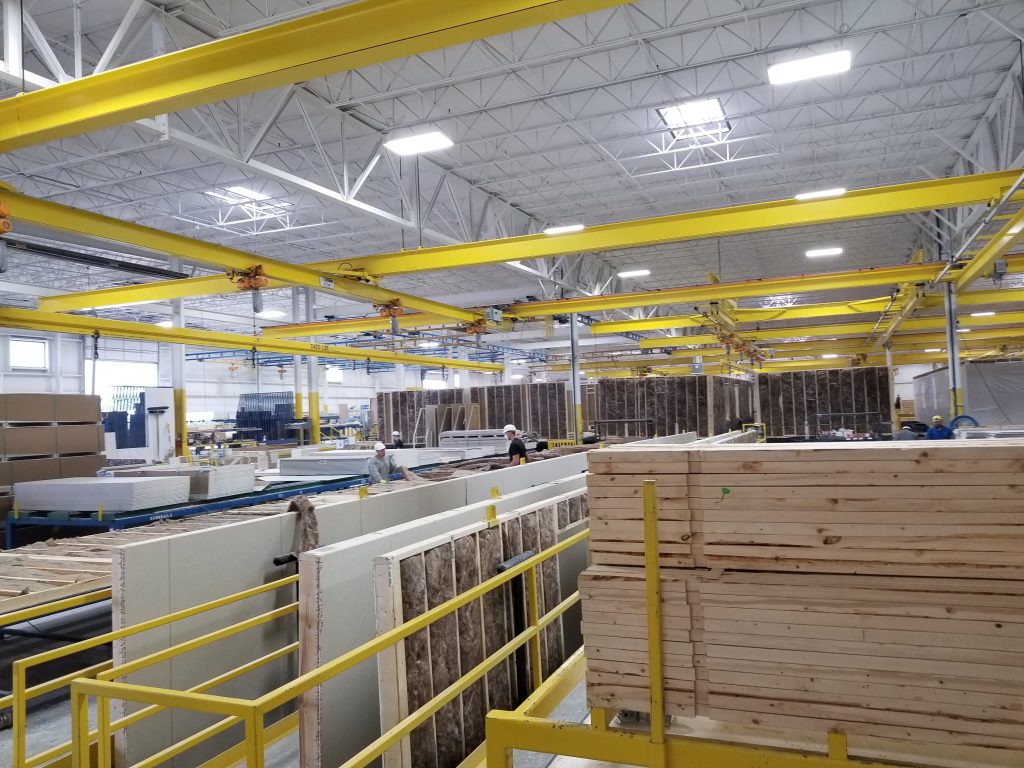
The new Clayton Homes factory in Wakarusa was a year old the day we visited. I and others from the MH industry looking for a tour, including Bill Sheffer and Darren Ing, the MMHA executive director and director respectively, gathered in a bright and modern team cafeteria.
Clayton Homes builders and office workers alike have access to the dining area, which has plenty of table and counter space, as well as TVs for checking in on the news or the game of the day perhaps.
After some conversation with Clayton folks, including with Wakarusa General Manager Jason Mickley about all the positive impact support and investment from Berkshire Hathaway has meant, we walked on to the gleaming new factory floor.
Clayton Home Builds by the Minute for Each Line
With 150 employees in the new factory Clayton Homes is able to turn out 14 new homes each day.
Building products are sourced through other Berkshire Hathaway companies when possible. This includes flooring and windows. With this kind of relationship and buying power, Clayton can keep costs down and pass that savings to the homeowner.
“We can control and drive our quality because they’re a part of this company,” Sales Manager Todd Fields said of the Berkshire relationship.
The Wakarusa plant has 18 Stations
A fair amount of bartering goes on between the Clayton builders each day.
“So we have 18 ‘buy offs’ internally,” Fields explained “If I have the walls and you’re building the floor, I get to ‘buy’ that floor from you. This is a primary driver of quality because each person up the line wants the best product to work with and be able to do their job with what they’re getting to the best of their ability.”
Fields pointed out how the new factory floor provides automated support that helps builders lift and strain less than typically do in older factories. Builders create jigs and other in-house measures to simplify the process. For example, they use a long jig with nail guns set in so interior floor trusses can be pinned together for the full width of the floor in a single shot.
Easing the heavy lifting allows builders to focus on their specialized skills as the homes move down the line. Fields said Wakarusa, at the time of the factory tour, was 150 days in to no-lost time injuries and hadn’t had an OSHA infraction for more than a year.
When the Roof Goes On a Full Interior Team Goes In
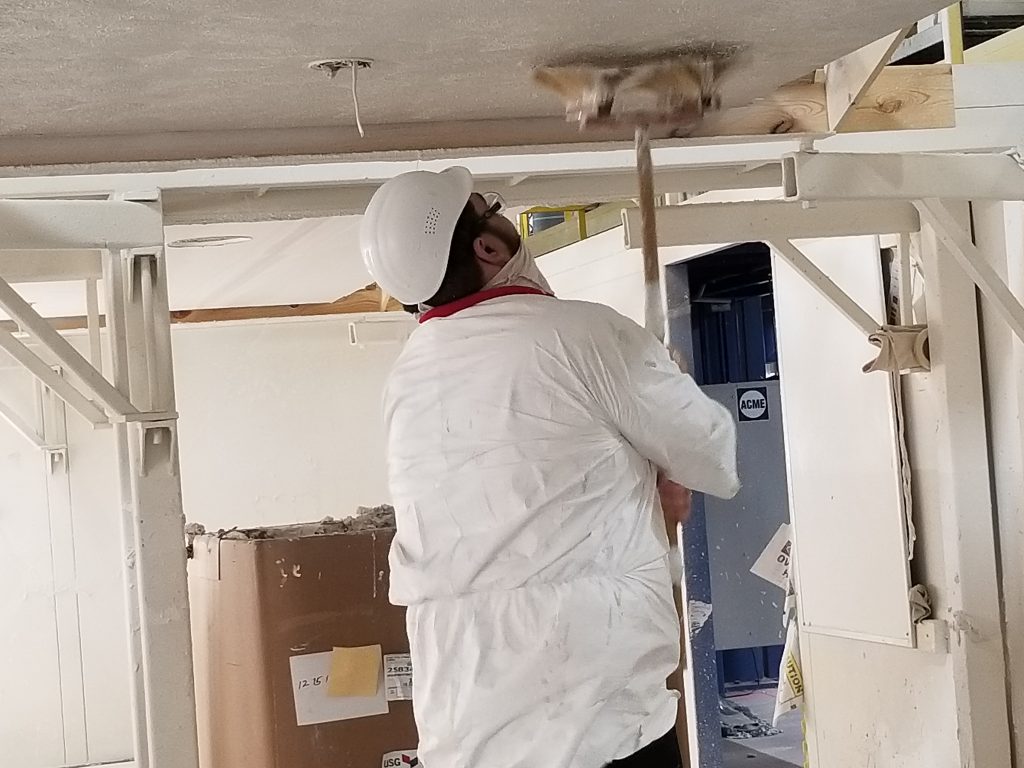
“As soon as the roof is set, it’s all hands on deck,” Fields said. “There’s much more energy on the home as it moves through the build, and that’ where our efficiencies really kick in.”
Matt Handshoe is the production manager at Wakarusa. He said Clayton has focused on team accommodations in plants largely because recruiting qualified builders is difficult.
“People can be hard to find and keep,” he said. “It’s the quality of the workplace and the experience that keeps our talent here. And our level of expertise on the floor is the top factor for achieving the quality construction we expect here.”
A high school graduate with a willingness to learn can start at Wakarusa for $12-15 per hour. The average wage in the plant is $20 per hour. A young motivated employee can quickly make $50,000 annually and learn a valuable trade.
Factory Expansion, Optimization is the Trend
CEO Kevin Clayton recently said the push is to improve every location rather than push resources to opening new plants. The growth mode for Clayton today means automating and expanding.
The company has invested more than $75 million to existing plants nationwide in last two years.
“You can add stations to a line, which generally allows you to build and move more floors,” Clayton said.